Plastic extrusion for tubing, profiles, and custom shapes
Plastic extrusion for tubing, profiles, and custom shapes
Blog Article
Comprehending the Basics and Applications of Plastic Extrusion in Modern Manufacturing
In the world of modern manufacturing, the method of plastic extrusion plays a crucial role. Deciphering the fundamentals of this procedure exposes the real flexibility and possibility of plastic extrusion.
The Principles of Plastic Extrusion Refine
While it may appear complex, the principles of the plastic extrusion procedure are based upon fairly uncomplicated concepts. It is a production process wherein plastic is melted and then shaped into a continuous account via a die. The raw plastic product, typically in the type of pellets, is fed right into an extruder. Inside the extruder, the plastic undergoes warm and pressure, causing it to thaw. The liquified plastic is then required with a shaped opening, referred to as a die, to develop a long, constant product. The extruded product is cooled and afterwards cut to the desired size. The plastic extrusion procedure is thoroughly made use of in different markets because of its effectiveness, cost-effectiveness, and adaptability.
Different Types of Plastic Extrusion Techniques
Structure upon the fundamental understanding of the plastic extrusion process, it is essential to discover the different methods associated with this production method. Both main strategies are profile extrusion and sheet extrusion. In account extrusion, plastic is thawed and created into a constant account, often made use of to produce pipes, rods, rails, and home window frameworks. On the other hand, sheet extrusion creates large, level sheets of plastic, which are usually further processed into items such as food packaging, shower curtains, and auto parts. Each strategy requires specialized equipment and exact control over temperature and pressure to guarantee the plastic keeps its shape during air conditioning. Recognizing these techniques is key to making use of plastic extrusion effectively in modern-day production.

The Function of Plastic Extrusion in the Automotive Market
An overwhelming majority of components in modern-day cars are products of the plastic extrusion process. This process has actually reinvented the auto sector, changing it into a more reliable, economical, and flexible production industry. Plastic extrusion is largely used in the manufacturing of different auto components such as index bumpers, grills, door panels, and dashboard trim. The procedure offers an uniform, regular outcome, enabling makers to produce high-volume get rid of excellent accuracy and minimal waste. The agility of the extruded plastic components adds to the overall decrease in lorry weight, enhancing gas effectiveness. In addition, the toughness and resistance of these components to warmth, cool, and influence improve the long life of vehicles. Thus, plastic extrusion plays a pivotal function in automotive manufacturing.
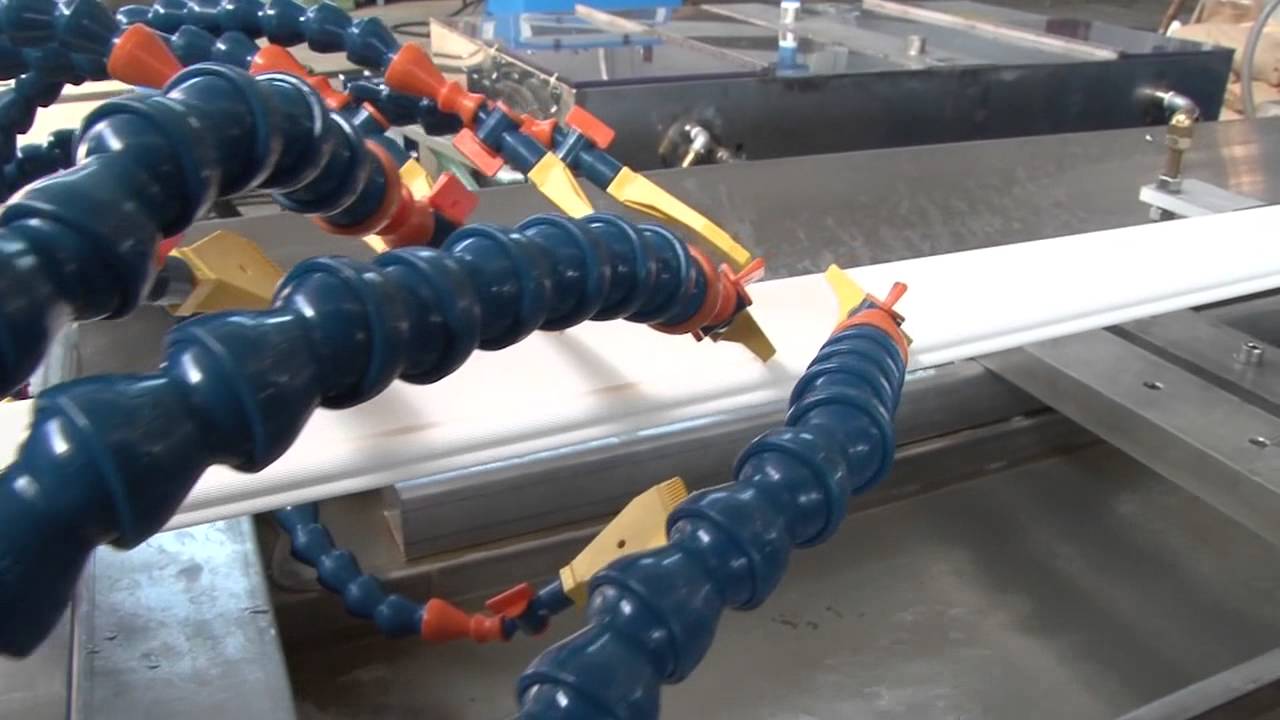
Applications of Plastic Extrusion in Consumer Product Manufacturing
Beyond its considerable influence on the automobile industry, plastic extrusion proves similarly reliable in the realm of customer items manufacturing. The versatility of plastic extrusion permits producers to create and create complicated forms and dimensions with high accuracy and efficiency. The versatility, versatility, and cost-effectiveness of plastic extrusion make it a preferred option for several customer goods suppliers, contributing substantially to the sector's development and development.
Environmental Effect and Sustainability in Plastic Extrusion
The prevalent usage of plastic extrusion in making invites scrutiny of its ecological implications. Effective equipment decreases power use, while waste administration systems recycle scrap plastic, reducing raw product demands. In spite of these improvements, further innovation is required to reduce the environmental impact of plastic extrusion.
Final thought
In conclusion, plastic extrusion plays an important role in modern-day manufacturing, especially in the auto and durable goods sectors. Its adaptability enables for the manufacturing of a vast array of elements with high precision. Its potential for recycling and growth of biodegradable see page products supplies an encouraging method in the direction of sustainable techniques, thereby attending to ecological concerns. Recognizing the essentials of this procedure read this article is essential to maximizing its applications and benefits.

The plastic extrusion procedure is extensively used in different sectors due to its convenience, performance, and cost-effectiveness.
Building upon the standard understanding of the plastic extrusion process, it is essential to discover the different techniques entailed in this production approach. plastic extrusion. In contrast, sheet extrusion creates huge, level sheets of plastic, which are typically more processed into items such as food packaging, shower drapes, and cars and truck parts.An overwhelming bulk of components in contemporary vehicles are items of the plastic extrusion procedure
Report this page